Od 1. října se generální ředitel společnosti Siemens Česká republika, pan Eduard Palíšek, ujal i funkce ředitele Operating Company Digital Industries. Velký rozhovor s ním jsme sice začali právě tímto tématem, velmi rychle jsme se ale dostali k přínosům digitalizace pro český průmysl, k nutné změně myšlení konstruktérů, i k tomu, kde si střední a malé firmy mohou vše potřebné vyzkoušet.
Proč vlastně došlo ke sloučení funkcí generálního ředitele Siemens a ředitele Digital Industries?
Před zhruba pěti lety nastartoval Siemens svůj program Vize 2020, který po úspěšném naplnění, navíc v předstihu, rozšířil o Vizi 2020+. Hlavním cílem je zvýšit flexibilitu jednotlivých oblastí podnikání v rámci společnosti. Celá korporace by měla zeštíhlet do pružnější organizace, která bude schopna rychle reagovat v každé oblasti podnikání, ať jde o průmysl, infrastrukturu, nebo energetiku. Siemens se proto rozhodl vytvořit tři tzv. Operating Companies, velké, jasně zaměřené jednotky s vysokou mírou autonomie. Jde o Digital Industries, Smart Infrastructure a Gas & Power.
Dále vznikly tři strategické společnosti – Siemens Mobility, Siemens Healthineers, tedy zdravotnická technika, a Siemens Gamesa, což jsou větrné elektrárny. Tyto oblasti procházejí různými cykly, je tedy zapotřebí mít v rámci jednotlivých Operating Companies větší autonomii. Spolu s tím přichází i změna řízení. Je logické a efektivní, aby dominantní část byznysu Siemens byla spojena s funkcí ředitele Siemensu v dané zemi. Česká republika je velmi průmyslová země a divize Digital Industries představuje největší část společnosti Siemens v ČR, proto je přirozené, že se ujmu právě jí. A díky tomu, že na kolegy v dalších Operating Companies budu moci delegovat více úkolů, uvolnil se mi prostor, který věnuji právě řízení Digital Industries. Z konglomerátu, který byl vystavěn na hierarchických strukturách, se stává společnost, která může nést až prvky startupových organizací. To je pro firmu této velikosti zcela unikátní. Vždyť Siemens má jen v Česku 12 tisíc zaměstnanců v osmi výrobních závodech či obchodních a vývojových organizacích. Působíme tu 129 let a takto zásadní změna nikdy v Siemensu neproběhla. Mám obrovské štěstí, že jsem její součástí.
Pomáhá vám při této změně digitalizace, přechod od hmoty k informaci?
Digitalizace je jedním z pilířů a hlavním rozvojovým směrem nejen Siemensu, ale celé průmyslové sféry a prosazujeme ji i interně ve svých procesech. Pokud je možné uplatnit umělou inteligenci nebo administrativní automatizaci, uplatňujeme je. Například v účetnictví máme softwarové roboty, kteří odstraňují rutinní práci. Lidé se v procesu budou moci spíše než jednoduchému zpracování dat věnovat jejich interpretaci, kreativním, analytickým a syntetickým činnostem, na které někdy nezbýval čas.
„Digitalizace přináší ohromnou flexibilitu. Musíte o ní ale přemýšlet správně.”
Eduard Palíšek, ředitel společnosti Siemens a Operating Company Digital Industries
A jak se digitalizace projeví v českém průmyslovém prostředí?
Česká republika je vysoce industrializovaná země. To má své přínosy, příležitosti i rizika. Část našeho průmyslu dodává finální výrobky nebo vyrábí komponenty pro finální výrobce. Nedá se říci, že jeden směr je dobrý a druhý špatný. Oba jsou potřeba a je na každém z podnikatelů, na co si troufá. Digitalizace pomůže oběma směrům. Firmám, které dodávají finální výrobky, umožní pružně a efektivně reagovat na individuální požadavky svých zákazníků a zvyšovat tak přidanou hodnotu svých výrobků. Firmám, které jsou součástí dodavatelského řetězce, pomůže kompenzovat postupné vymizení komparativní výhody založené na relativně nižší ceně práce a navíc pro ně digitalizace bude nezbytnost. Dodavatelské firmy jsou většinou navázány na společnosti v západní Evropě, kde digitalizace v průmyslové výrobě postupuje velmi rychle. Odběratelé nebudou do budoucna spolupracovat s firmami, které se nebudou schopny napojit na jejich digitální dodavatelský řetězec. Potřebují, aby celý jejich hodnotový řetězec fungoval digitálně a pružně. To dodavatelské firmy donutí k tomu, aby na digitální vlnu nastoupily, nebo v něm budou postupně nahrazeny jinými. Opravdu je to takto černobílé. Nebude to ze dne na den, dnes ještě někdo cítí nedostatek zaměstnanců, ale za chvilku komparativní výhoda zmizí a ukáže se, jak je kdo připraven uspět v globálním konkurenčním prostředí.
Jak to bude probíhat?
Digitalizace přinese potřebnou flexibilitu. Není ale možné zůstat jen u digitalizace produktu jako takového, je zapotřebí digitalizovat celý výrobní proces i provoz výrobku. Od počátku návrhu výrobku, od digitálního dvojčete produktu, přes digitalizaci výrobní linky až po monitorování chování výrobku při jeho použití. S dnešními technologiemi je možné navrhnout celou továrnu v digitálním prostředí. Všechny parametry lze dimenzovat tak, aby odpovídaly vašim požadavkům. A co je velmi důležité: když máte digitální model výrobku i výrobního procesu, je každá další změna jen inkrementální změnou. Můžete snadno změnit produkt a navíc, díky silným simulačním nástrojům, do kterých Siemens hodně investoval, můžete v digitálním prostředí simulovat řadu věcí, které byste jinak museli testovat v reálném světě. Tím výrazně zvýšíte rychlost, snížíte náklady a jste výrazně pružnější. A v tu chvíli budete jen krůček od toho, abyste flexibilně dokázali svůj produkt modifikovat a vyrábět na základě požadavku zákazníka. Jestliže totiž máte výrobek, který jste schopni modifikovat takřka lusknutím prstů, a na stejném principu máte vystavěnou výrobní základnu, jste schopni rekonfigurovat svou výrobu podle okamžitých potřeb. Přímým vstupem pro váš výrobní proces tak může být přímo objednávka z e-shopu. A to je cíl. Přinést digitalizaci do výroby v takové míře, že bude schopna reagovat na poptávku okamžitě a bez potřeby velkých změn a investic. Výrazně se zvýší efektivita, protože se nebude vyrábět na sklad, zvýší se i přidaná hodnota a celý hodnotový řetězec bude navíc i ekologicky udržitelnější.
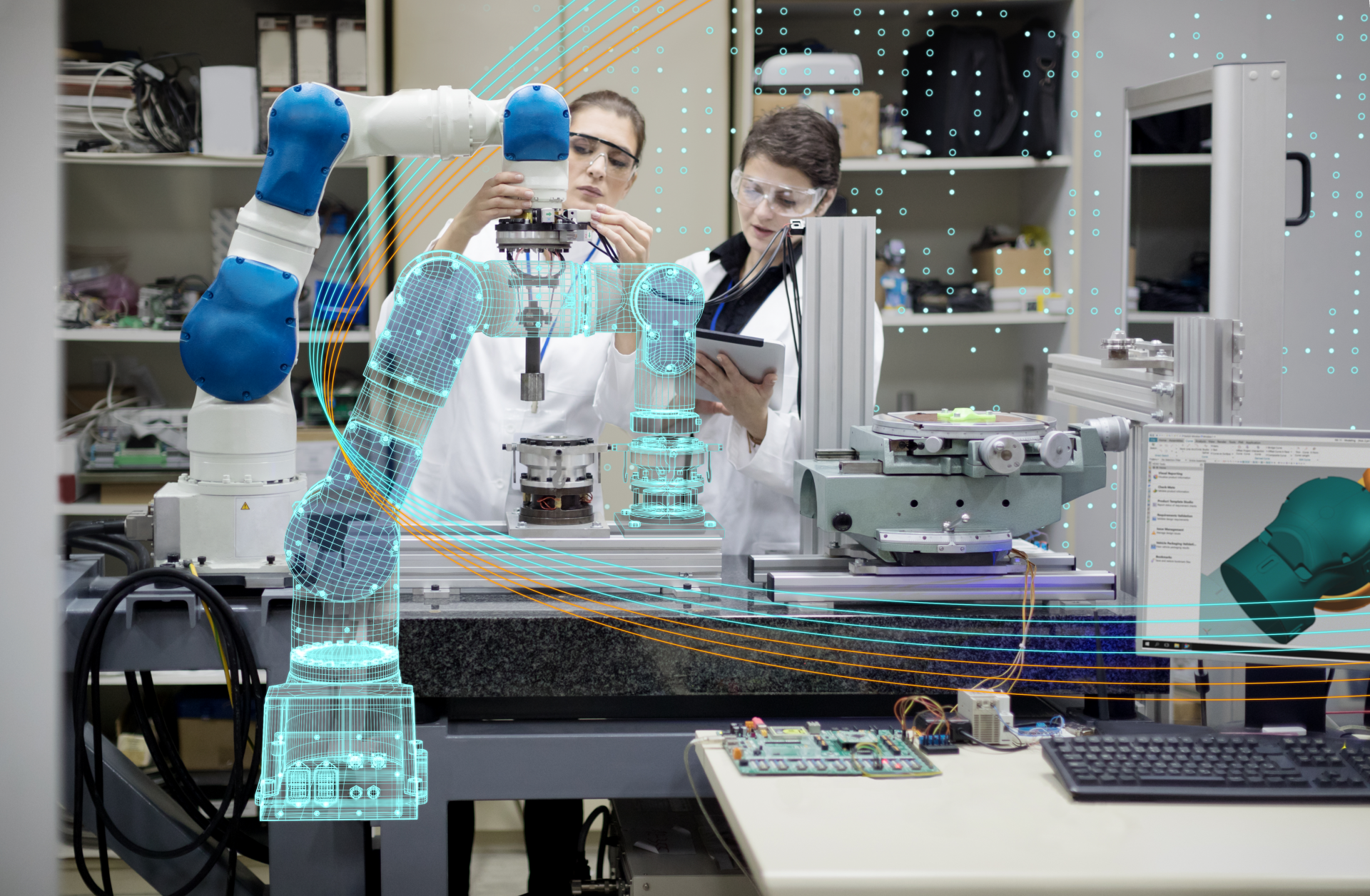
Co pro to budou muset firmy změnit?
Jedna z cest, která přináší velkou flexibilitu, je aditivní výroba – lidově se jí říká 3D tisk. Pro vytvoření výrobku nepotřebujete kromě vhodných materiálů nic jiného než digitální model. Dnes už lze kombinovat různé materiály, třeba i takové, které se mohou následně rozpustit, a díky tomu mohou vzniknout i velmi komplikované tvary. Můžete vyrobit struktury, které byste klasickou cestou nebyli schopni udělat. Když se podíváte na součásti, které vznikají aditivní cestou, jsou některé z nich standardní cestou nevyrobitelné, nebo vyrobitelné, ale za velmi vysokých nákladů.
Je ale aditivní výroba dostatečně efektivní? Dokáže konkurovat tradičním metodám?
Často se setkávám s tím, že někdo říká, že aditivní výroba je pomalá. Může to tak být, pokud ji budeme porovnávat na úrovni jednotlivé operace tradičního, třeba třískového obrábění. Ale pokud se na proces vzniku výrobku podíváte celistvě – od návrhu až po jeho uvedení do provozu, pak už této nové technologii výroby těmi tradičními konkurovat nelze. Nově konstruované součásti výrobku vznikají na principu inteligentního adaptivního designu, který vytváří tvary a struktury podřízené funkci, nikoli omezením vyrobitelnosti klasickými metodami. Když se tedy podíváte na mechanické vlastnosti výrobku, na flexibilitu konstrukce a výroby holisticky, nejen pohledem jedné konkrétní výrobní operace, je to jednoznačné.
Jak to?
Díky digitalizaci se nám otevírá úplně nový fascinující svět s naprosto odlišným přístupem k tvorbě produktu. Jsem vystudovaný strojař a učil jsem se konstruovat ze základních tvarů. Hranol, válec, plech. Z nich jsme soustružili, svařovali, ohýbali, frézovali. Museli jsme dbát na to, jestli jsou materiály spojitelné, na množství odpadu při zpracování. Byla tam celá řada omezujících faktorů. Design byl podřízený materiálu. Dnes se ale při návrhu některých prvků inspirujeme přírodou. Pomocí nástrojů, které Siemens uvedl na trh, nepostupuje konstruktér od materiálu, ale od požadovaných mechanických funkcí výrobku. Součástku popíše pomocí jejích vlastností: tady se má přenášet krouticí moment, tady je zapotřebí takový a takový efekt. Software potom s pomocí simulačních a analytických metod, metody konečných prvků a dalších matematických nástrojů tyto funkce „obalí“ materiálem. Když vidíte součástky navržené těmito novými metodami, vypadají téměř jako přírodní prvky. Říkám tomu organický design. Podívejte se například na lidskou lýtkovou kost. Kdyby ji navrhoval klasický konstruktér, byla by to nejspíš trubka s navařenými klouby nahoře a dole. Ale ve skutečnosti vypadá naprosto jinak. Má nepravidelný tvar, v různých místech má různou tloušťku. Materiál je jen tam, kde je z mechanických důvodů zapotřebí. Stejně postupuje i inteligentní software. Umístí materiál jen tam, kde je potřebný kvůli fyzikálně-mechanickým požadavkům na výrobek. Vznikají tak velmi komplexní složité povrchy a struktury, standardními metodami nevyrobitelné.
Kde se takový přístup mohou firmy a konstruktéři naučit?
Například v Testbedu – sdílené laboratoři pro Průmysl 4.0. První funguje již dva roky v Praze při ČVUT v nové budově CIIRC v rámci Národního centra Průmyslu 4.0. Jedná se o unikátní platformu pro otevřenou spolupráci napříč průmyslem a akademickou sférou. Jsme zakládajícím členem NCP 4.0 a jedním z hlavních koncepčních partnerů. V Testbedu působí celá řada šikovných českých firem, které do něj vnášejí své know- -how. Vzniklo tak experimentálně-vědecké pracoviště, kde mohou studenti realizovat své ročníkové projekty, diplomové i disertační práce a pedagogové mohou aktualizovat své znalosti o digitalizaci průmyslu. Zároveň tam mohou přijít i malé a střední firmy, které jinak nemají přístup k potřebnému know-how. Zde mohou nalézt inspiraci, vidět referenční projekty a ověřit si své koncepty. Podobné centrum demonstrující možnosti Průmyslu 4.0 je i v Brně, otevření dalšího připravujeme v Ostravě a jednáme o vzniku Testbedů i v Plzni a Liberci.
Digitalizace ovšem znamená i otevírání se vnějšímu světu. Jak bezpečný tento proces je? 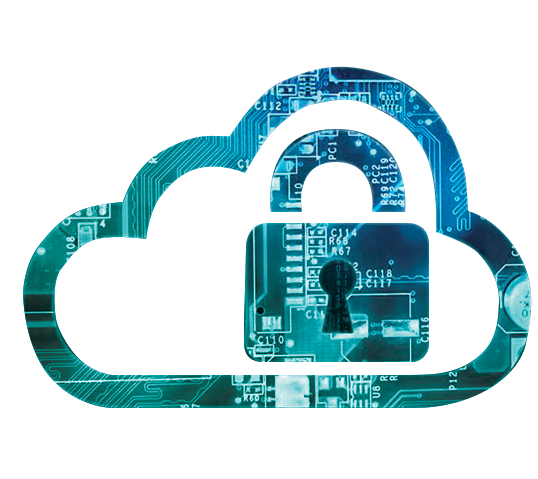
V našem systému MindSphere, jediném otevřeném operačním systému pro internet věcí svého druhu, probíhá přenos informací stejně bezpečně jako přenos dat do banky. A pracujeme i na dalších způsobech, jak bezpečnost zvýšit. Jde například o edge computing, kdy řada výpočtů probíhá přímo v koncových zařízeních nebo lokálně v jejich těsné blízkosti. Přenáší se jen dílčí informace, případně již zpracovaná data. Decentralizujete tak výpočetní kapacitu a minimalizujete přenos strukturovaných dat, při kterém by bylo možné cenná data zcizit, změnit či zneužít. To má vliv i na zvýšení rychlosti. Když totiž chcete řídit autonomní systémy v reálném čase, musíte mít velmi vysoké přenosové rychlosti.
Zastaví se vývoj na úrovni digitální továrny?
Rozhodně ne. V rámci Národního centra Průmyslu 4.0 už nyní probíhá projekt RICAIP, zaměřený na virtuální distribuované továrny.
Virtuální továrny?
Trend digitalizace se nezastaví. Svou továrnu si nejenže budete moci kompletně sestavit na základě digitálních dvojčat, ale v budoucnosti možná vznikne systém, kde se jednotlivé výrobní továrny budou specializovat na určité druhy operací. Nad nimi pak vzniknou virtuální továrny, které budou využívat jejich zdroje a nebudou muset neustále reinvestovat kvůli změně výrobního programu. Pokud bude virtuální továrna potřebovat speciální stroj, dostupný v jedné konkrétní fyzické továrně, zakomponuje ho do svého procesu výroby. To může být další zásadní změna výrobního paradigmatu. V dnešním modelu vymyslíte výrobek, zpracujete dokumentaci a zadáte jeho výrobu. Někdo pak na základě toho postaví linku, vyrobí a dodá to, co požadujete, vy výsledek zkontrolujete a dál s ním pracujete. Ve virtuální továrně budete jednotlivé virtuálně propojené zdroje konfigurovat sám podle toho, co chcete vyrábět. Nejde o outsourcing. Na celek se díváte jako na vlastní továrnu, jen s decentralizovanými zdroji.
Takže někde bude třískové obrábění, někde aditivní výroba, někde testovací laboratoř a budu si to skládat podle toho, co právě potřebuji?
Fyzická továrna vám zprostředkuje technickou kapacitu, konfigurovat stroje ale budete sám. Můžou tak vzniknout i nové obchodní modely – třeba poskytování strojového času výrobních strojů. A tady se vracíme k tomu, že je klíčová digitalizace. Všechny součásti virtuální továrny budou muset být na stejné digitální úrovni.