Nové predikční systémy budou schopny rozpoznat závady již v jejich zárodku nebo dokonce ještě před ním. V plynových elektrárnách by například pohybové senzory mohly měřit opotřebení turbíny a naměřené údaje předávat do databáze. Počítač by pak tato data průběžně analyzoval a v případě, že by byla překročena kritická teplota ve spalovací komoře, spustil by alarm.
Velkou část z tohoto ohromného množství dat však doposud zůstává nezanalyzována, protože se jedná o data nestrukturovaná, v nichž lidé nerozpoznají více než virtuální chaos. Avšak s pomocí speciálních algoritmů pro práci s tzv. big data by se v tomto chaosu mohly objevit dosud nepozorované vztahy a informace na nich založené by například mohly pomoci průmyslovým firmám při optimalizaci výroby a servisu.
Ihned k dispozici
Podle konzervativních odhadů by se s novými analytickými nástroji zkrátil čas, který technici potřebují k získání dat potřebných k provedení opravy, minimálně o 25 %. „Protože průměrně 80% pracovního času technici stráví sbíráním dat, odhadujeme, že by bylo možné každoročně ušetřit jen na servisu turbín přes milion eur,“ domnívá se Steffen Lamparter ze Siemens Corporate Technology (CT). Analýzy tohoto druhu již byly provedeny na nejnovější plynové turbíně třídy H od společnosti Siemens. Inženýři tak nyní získávají data o turbíně okamžitě a bez ohledu na to, kde se zrovna nacházejí. Turbína je vybavena 1500 senzory, které měří její nejdůležitější činnosti a vlastnosti, jako je teplota, tlak nebo složení plynu.
Skryté vztahy závad
Společnost Siemens plánuje, že vytvoří systém, který bude zkoumat vztahy mezi závadami, jež se na strojních zařízeních vyskytnou, a součástkami, které jsou na nich nainstalovány. „V budoucnosti budou mít konstruktéři ke všem těmto datům přístup, a když budou vybírat součástky pro nová zařízení, budou si moci zjistit, jak tyto součástky fungují v praxi,“ vysvětluje Steffen Lamparter. Tento vývoj v současné době probíhá v rámci evropského výzkumného projektu Optique, na němž se podílejí průmyslové firmy, jako je Siemens nebo norský Statoil, a také několik univerzit. Cílem je vytvořit algoritmy a technologie, které by učinily hledání v komplexních databázích efektivnějším, tzn. propojily by různé zdroje dat a databáze a dokázaly by v nich najít užitečné informace. Optimalizace dat pomůže zlepšit preventivní servis elektrárenských turbín a přispěje k tomu, že elektrická soustava pak bude odolnější proti výpadkům. „V naší části projektu nejde o práci s obrovským množstvím dat, servis turbíny vytváří denně jen 30 GB dat a celá databáze má celkem 10 TB,“ popisuje Steffen Lamparter. Mnohem obtížnějším úkolem je integrovat různé databáze do tzv. data poolu, který se neustále mění a rozšiřuje. „Své výpočty proto musíme neustále aktualizovat. To je zásadní úkol, pokud chceme získávat výsledky v reálném čase,“ dodává Steffen Lamparter. Nestrukturovaná data, například chybová hlášení v textové podobě, mohou být kombinována se strukturovanými daty, jako jsou údaje o chodu stroje. Textové a obrazové analýzy mohou transformovat textové, audio-, video- a obrazové soubory do analyzovatelných dat. Problémem je, že velké množství zdrojů dat a formátů musí být logicky spojeno tak, aby na základě takto vzniklých informací mohly být učiněny závěry o možných poruchách a závadách. Projekt Optique je teprve na počátku – zahájen byl v listopadu 2012 a potrvá do konce roku 2016. Společnost Siemens si od něj mnoho slibuje. „Věříme, že výsledky projektu budou přenositelné i na další aplikace big data,“ říká Gerhard Kress ze Siemens CT, kde má na starosti koordinaci projektů big data.
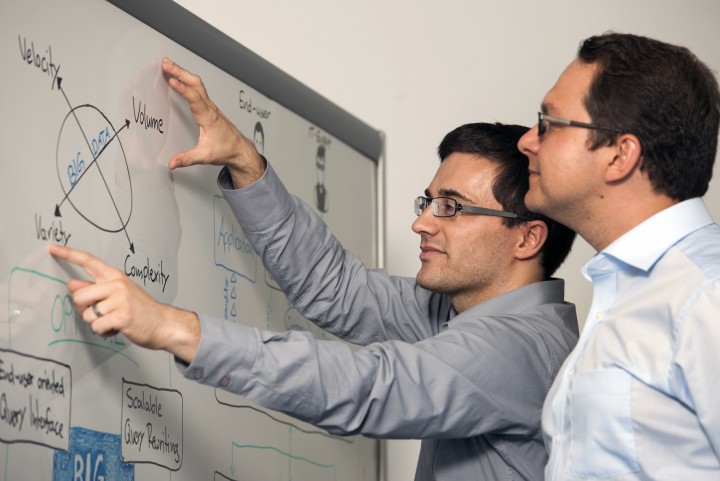
Kdy to opravíme?
Podobný přístup jako inženýři z energetické divize společnosti Siemens zvolili i specialisté z divize Healthcare. Ti vyvinuli systém, který dokáže vypočítat pravděpodobnost, jakou klíčovou součástku, například rentgenovou trubici v počítačovém tomografu, může postihnout závada. Tomografy jsou vybaveny senzory, které sledují parametry, jako je elektrický proud v trubici, rotace anody či teplota oleje. Monitorovací software neustále přenáší data do servisního centra společnosti Siemens. „Tato data umožňují našim kolegům používat komplexní algoritmy k výpočtu pravděpodobnosti závady během příštích několika dnů,“ pokračuje Gerhard Kress. Díky tomu se nyní mohou servisní technici domluvit s radiology na termínu opravy tak, aby její vliv na provoz zařízení byl co nejmenší. Podle Gerharda Kresse by se v budoucnu díky novým vyhledávacím postupům mohly v „big data pools“ objevit vztahy, jejichž význam pro medicínskou praxi lze dnes jen těžko odhadnout. V tomto směru je však třeba vykonat ještě velké množství výzkumné práce.