Byla to vlastně spanilá jízda po severu republiky. Frenštát pod Radhoštěm, dvakrát Mohelnice, Letohrad a Trutnov. To je pět lokalit, které jsme při svém putování za Průmyslem 4.0 v Česku navštívili. Ani v jednom případě se nejedná o nějakou umělou „demonstrační“ továrnu. Všechno to jsou aktivní závody, které denně chrlí skutečné produkty pro světové trhy. Ve svém oboru patří mezi giganty a tvoří páteř výrobní základny koncernu Siemens. Výroba tu proto skutečně musí hladce a efektivně fungovat. Na neověřené experimenty a umělé příkrasy není prostor. Ani jeden ze závodů navíc nevyrostl na zelené louce. A ani jeden není čistě robotizovaná sterilní továrna. Ve všech hraje roli i manuální práce. Při plánování implementace prvků Průmyslu 4.0 proto musel management brát v potaz stávající budovy, zavedené technologie a své zaměstnance. A implementaci samozřejmě musel provést s co nejmenšími dopady na plynulost výroby. Zákazníci nečekají a plán výroby je třeba plnit. Na hraní tu není čas. Siemens nám zkrátka nenastrčil žádné pozlátko, ale pozval nás do pěti továren, kde potkáte hučící stroje, dělníky v montérkách a vysokozdvižné vozíky plnící kamiony fyzickými produkty. Při procházení hal vás napadá, že podobně vypadají desítky dalších elektrotechnických a strojírenských továren v Česku. Řeší podobné problémy, mají podobná očekávání, rozhodují se podle podobných priorit a hledají vlastně podobná řešení. Naše návštěva ukázala, že i pro ně jsou prvky Průmyslu 4.0 provozně výhodné, technicky dosažitelné a ekonomicky ospravedlnitelné.
INTELIGENTNÍ TOVÁRNA V MOHELNICI
Mohelnický závod Siemens Elektromotory je největším závodem na výrobu nízkonapěťových asynchroních elektromotorů v Evropě. Se svými 62 budovami zabírajícímu plochu 30 hektarů je zároveň nejrozlehlejším výrobním areálem koncernu Siemens na světě. Jeho přibližně 2 000 zaměstnanců každý pracovní den dokončí okolo 4 000 elektromotorů, které následně putují doslova do celého světa. Kvalitu, efektivitu a flexibilitu tu pomáhají zvyšovat myšlenky Průmyslu 4.0. A to v takovém rozsahu, že se do Mohelnice jezdí dívat návštěvy, a závod by se měl brzy zařadit do nové generace digitalizovaných inteligentních továren.
„Implementace prvků Průmyslu 4.0 do výroby elektromotorů spočívá zejména v míře využití dílčích chytrých řešení. V našich podmínkách jde o digitální podporu všech konstrukčních, technologických a výrobních procesů,“ vysvětluje ředitel závodu Pavel Pěnička. Aby to nebylo zase tak jednoduché, tak veškeré kroky jsou v rámci digitálního podniku plynule propojeny nepřetržitým tokem dat – od návrhu produktu přes výrobu až po expedici. I díky tomu dokážou v Mohelnici vyrábět v masovém rozsahu individualizované produkty, které si zákazníci vybírají z 65 000 aktivních variant.Prvním z prvků Průmyslu 4.0, se kterým se v jedné z hal setkáváme, je elektronické sledování využití strojů. Prozatím se týká zhruba desetiny z celkových 2 500 činných výrobních zařízení. Zapojení elektronického obvodu do řídicího systému strojů umožňuje v reálném čase sledovat a vyhodnocovat efektivitu výroby, provádět analýzy a hledat vylepšení. Management dostává nezkreslené informace o aktuálním využití strojů a statistiky jejich provozu, což mu umožnuje redukovat ztrátové časy, identifikovat úzká hrdla a celkově zefektivňovat činnost závodu. Efektivita se sleduje i u manipulační techniky. 50 vysokozdvižných vozíků, tedy zhruba polovina závodní flotily, je vybaveno datovým rozhraním a přijímačem GPS. Po přihlášení k serveru tak můžete kdykoliv získat informaci, kde se vozíky pohybují, kdo je řídí a zda jsou využívány efektivně. Monitoring pomáhá lépe plánovat logistiku, spořit zdroje a vytěžovat techniku. Dodatečná funkce sledování nárazů zase přispívá k vyšší bezpečnosti práce a snižuje náklady na servis techniky. S optimalizací interní logistiky pomáhají také simulace materiálových toků. V Mohelnici pro ně využívají software z dílny Siemens. Simulace jim pomohla při kapacitním výpočtu využití tras interního milkrunu, při modelování úprav lakovny, kapacitním ověřování vícestrojových obsluh nebo při nákupu nových strojů pro obrobnu rotorů. Asi není třeba dlouze vysvětlovat, že ověření navrhovaných řešení ve virtuálním světě pomáhá předejít nákladným a často těžko odstranitelným chybám ve světě reálném. Na tohle máme teprve projekt, na kterém se pracuje, takže se nedá říct, že by to fungovalo. Určitě by se nemělo prezentovat, že to tu už máme, protože to není tak úplně pravda. Je to ideální stav, ke kterému teprve chceme dospět. Digitalizována byla samozřejmě také veškerá technická a výrobní dokumentace – od fáze vývoje a návrhu až po využití při výrobě a kontrole kvality. Na přínosy takového přístupu a centrální správy dat se podíváme na příkladech dalších závodů. Za zvláštní zmínku však stojí animovaná montáž komponent.
„Digitalizovaná byla samozřejmě také veškerá technická a výrobní dokumentace – od fáze vývoje a návrhu až po využití při výrobě a kontrole kvality.“
Dnes již více než 4 000 videí poskytují zaměstnancům animované návody k jednotlivým krokům montáže některých komponent elektromotorů. Systém je však použitelný i pro animaci montáže celého elektromotoru, což může dobře posloužit zejména u komplikovaných zákaznických provedení.
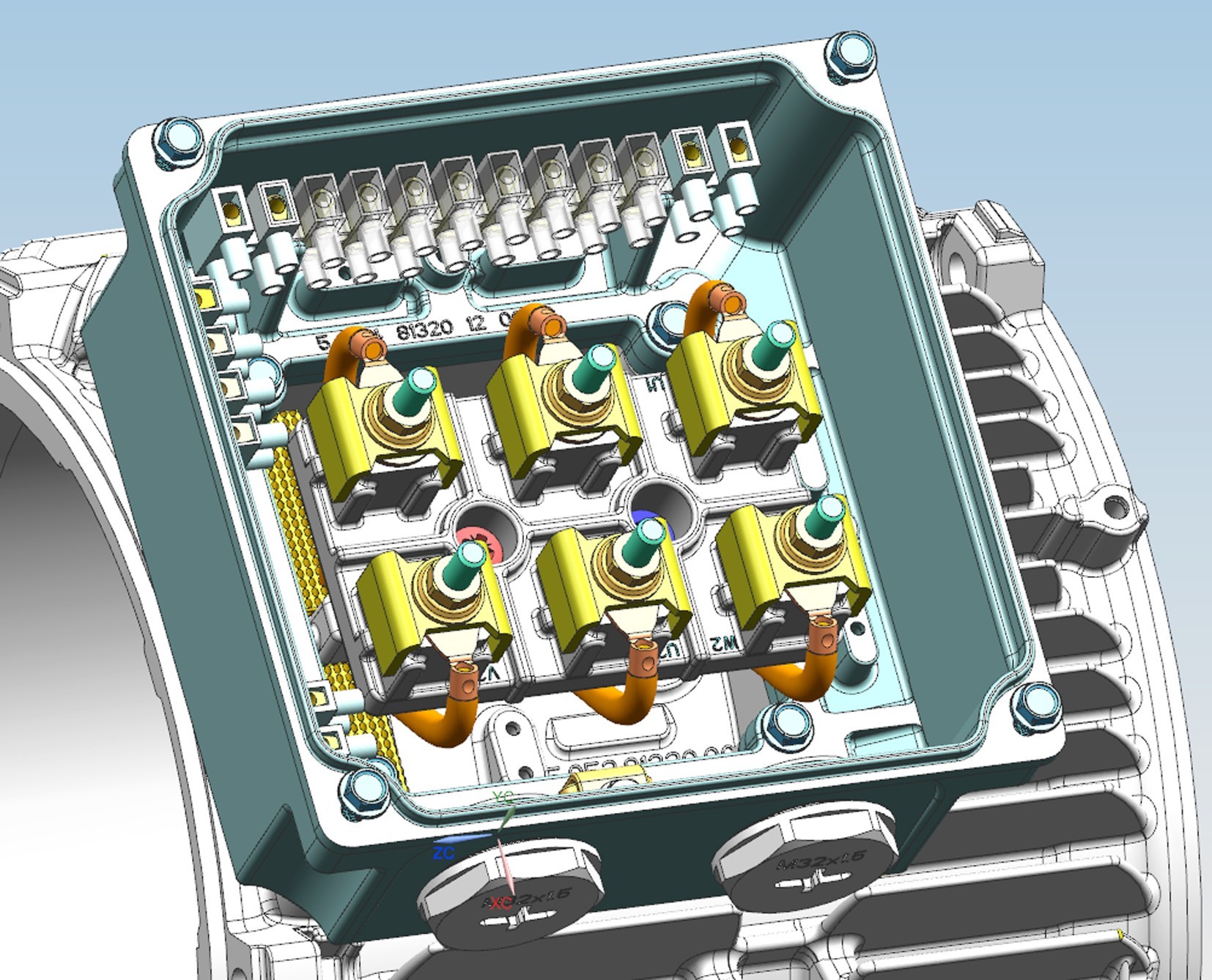
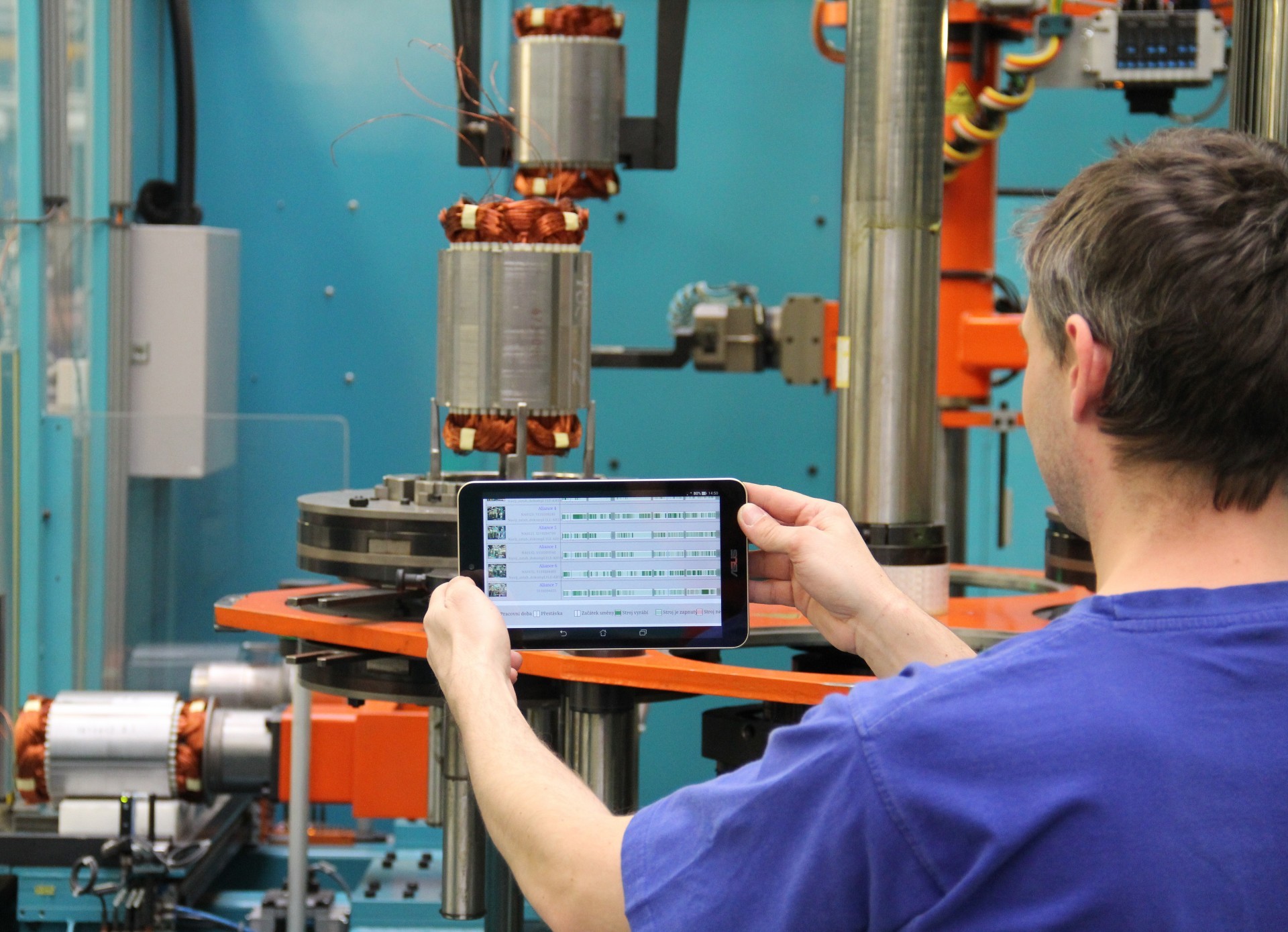
Přehlídku prvků Průmyslu 4.0 v Mohelnici uzavírá inteligentní systém řízení budov. Ten u tak rozsáhlého areálu dokáže významně snížit provozní náklady. Umožňuje monitorovat spotřeby energií a řídit všechny základní technologie budov z centrálního dispečinku. Podle aktuální spotřeby stlačeného vzduchu je tak optimalizován chod kompresorů. Centrálně je řízena také příprava teplé vody, navíc s využitím solárního předehřevu, vytápění nebo osvětlení. Tak například každé z LED svítidel používaných k osvětlování rozsáhlých mohelnických hal komunikuje s dispečinkem, hlásí mu své provozní hodiny, aktuální výkon i případnou poruchu. Podobné technologie mají Siemensu pomoci naplnit ambiciózní plán razantního snižování produkovaných emisí.
BEZOBLUSŽNÝ VOZÍK SLOUŽÍ VE FRENŠTÁTU
Frenštátský závod Siemensu dodává zákaznická provedení nízkonapěťových asynchroních eletromotorů osových výšek 225 až 315 mm. V tomto segmentu je největším evropským výrobcem. Motory odsud putují zejména do velkých investičních celků, především jako pohony čerpadel, kompresorů nebo vzduchotechniky. Závod, který za sebou má úspěšnou sedmdesátiletou historii, v posledních letech významně investoval do inovací v oblasti automatizace a digitalizace.
V roce 2013 tu jako první ve střední a východní Evropě uvedli do provozu automatizovaný vozík BT Autopilot. Ten zásobuje komponentami dvanáct výrobních pracovišť zdejší navijárny. Jeho navigaci samočinně obstarává software, v němž je naprogramováno upořádání provozu. Na základě požadavků jednotlivých pracovišť vozík přiváží palety s komponentami potřebnými pro kompletaci dalšího setu a odváží palety prázdné. Automatizace manipulační techniky zrychlila dodávky a pomohla se vypořádat se zúženým prostorem v důsledku rozšíření výroby. Současně snížila provozní náklady. Automatizovaný vozík BT Autopilot samočinně zásobuje jednotlivá pracoviště frenštátské navijárny potřebnými komponentami. Vystačí si s menším manipulačním prostorem a je rychlejší, spolehlivější a úspornější než vozíky s lidskou obsluhou.
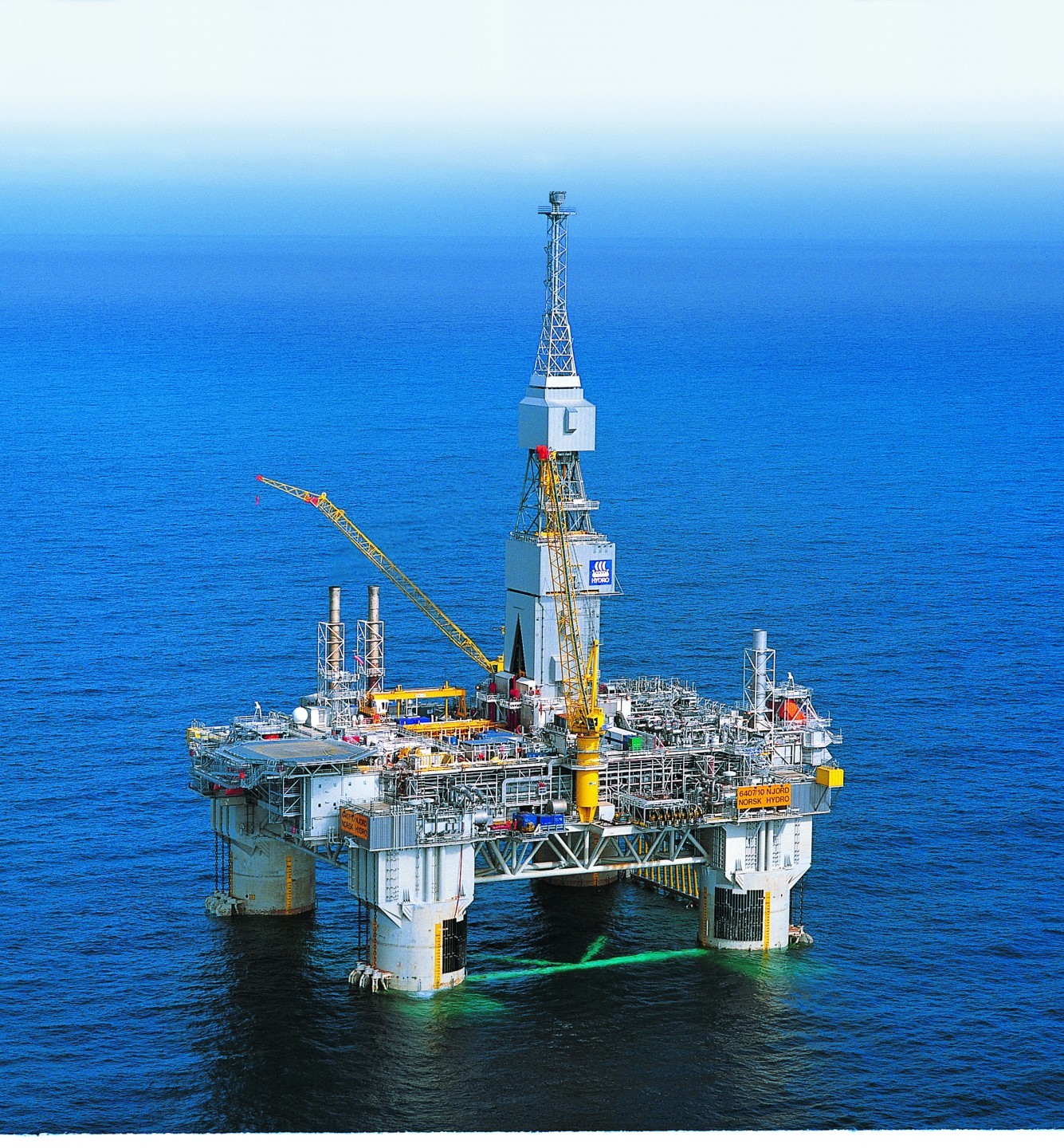
Ve Frenštátu také byla zavedena takzvaná bezpapírová výroba. Veškerá technická dokumentace a informace k výrobní zakázce putují závodem výhradně v elektronické podobě. I ve výrobě si je lze jednoduše zobrazit pomocí dotykových obrazovek. Podle zdejších zkušeností to významně zrychluje komunikaci mezi výrobními celky. Významnou inovací bylo též nasazení hlasového vychystávání ve skladu. To je založeno na rozeznávání lidského hlasu a naopak na interpretaci dat ve formě hlasu. Díky němu získávají pracovníci skladu pokyny pro prováděné operace výhradně hlasově, ze sluchátek. To jim uvolnilo ruce i zrak. Mohu se tak lépe soustředit na samotnou manipulaci se zbožím, jejich práce se zrychlila a současně je bezpečnější.
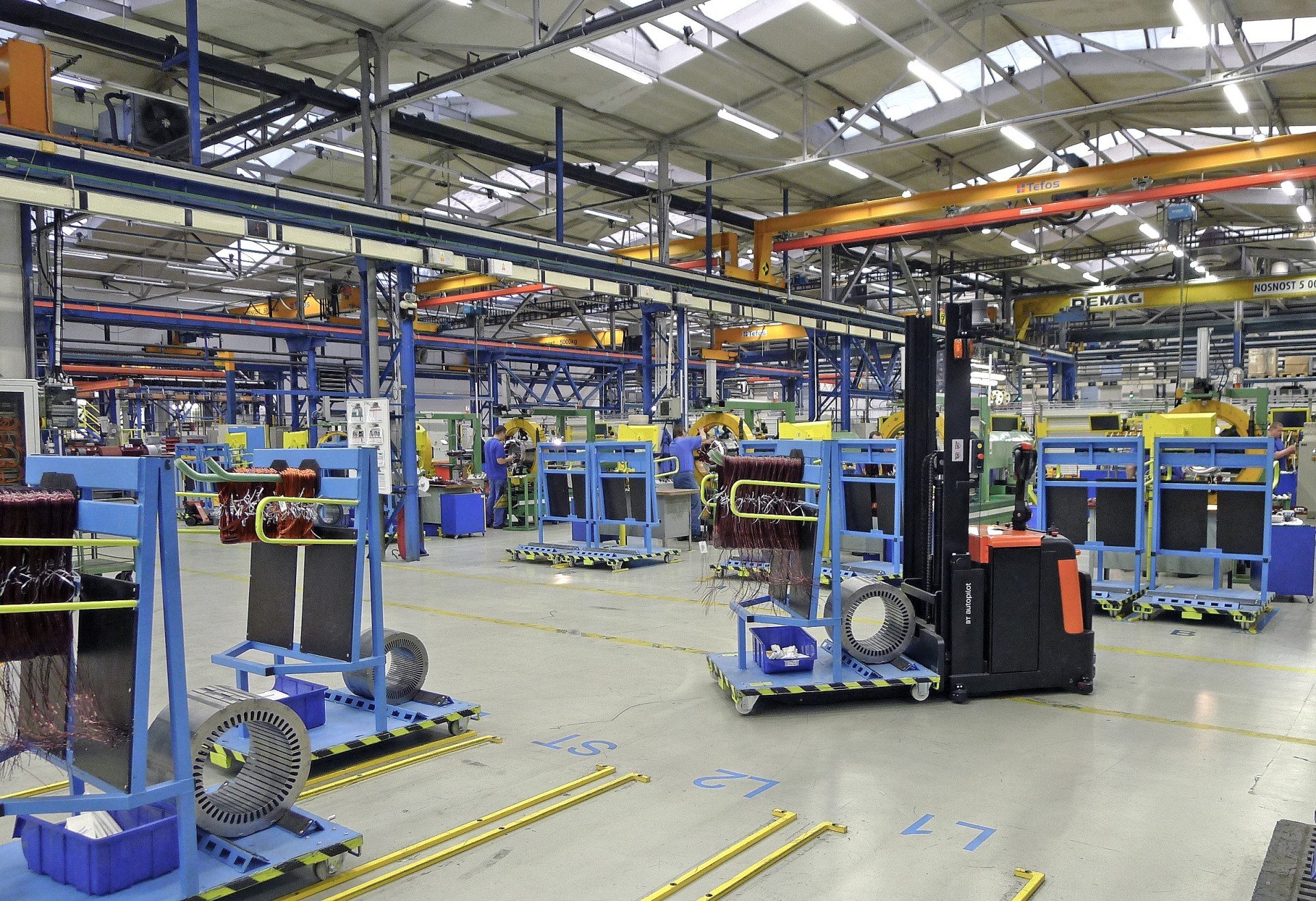
Ve frenštátském závodě se také zrealizoval projekt s názvem Sledování využití manipulační techniky, který má za sebou první výsledky. Jeho základem je vybavení vysokozdvižného vozíku provozními snímači a GPRS vysílačem, který přenáší data přes rozhraní do webové aplikace I_SITE. Jsou vytvořeny okruhy pracovníků pro zamezení neoprávněného použití. Každý řidič má v systému definovaný profil, který obsahuje identifikační kód, řidičské oprávnění pro definovanou skupinu vozíků a směnnost. Z jednotlivých vozíků se do systému přenášejí provozní údaje, jako jsou např. čas jízdy, čas zdvihů, stav trakčních baterií (doba nabíjení, změny kapacity) a nárazů stroje. Z těchto parametrů aplikace následně předává údaje, které vedou k lepšímu využití stroje, baterie nebo skupin strojů. Opatření tohoto projektu vedla ke snížení počtu manipulační techniky o 6 %, snížení nákladů na školení řidičů o 23 %, snížení nákladů na servis o 3 % a současně se finančně odrazila na produktivitě závodu. Důležitou oblastí je zvýšení bezpečnosti práce. Přispívá k tomu vyhodnocování četnosti nárazů, kdy se rozlišují tři stupně nárazů s možností blokace vozíku. Data slouží jako podklad pro analýzu příčin a ke stanovení nápravných opatření.
„Významnou inovací bylo též nasazení hlasového vychystávání ve skladu. To je založeno na rozeznávání lidského hlasu a naopak na interpretaci dat ve formě hlasu. Díky němu získávají pracovníci skladu pokyny pro prováděné operace výhradně hlasově, ze sluchátek.“
V TRUTNOVĚ PROVÁZÍ VÝROBEK QR KÓD
Automatizace je již několik desítek let nedílnou součástí výroby také v trutnovském závodě Siemens Nízkonapěťová spínací technika. Ve dvou halách ze vyrábějí elektromechanické spínací přístroje a relé a osazují plošné spoje. Posledním technologickým posunem je digitální propojení jednotlivých částí výrobních linek. Jejich jednotlivá zařízení komunikují se servery, na nichž se nacházejí data potřebná pro výrobu. „V tomto rozšíření automatizace, která je jinak známa již několik desetiletí spatřujeme naplnění prvního kroku ke konceptu průmyslu 4.0,“ říká David Krynek, vedoucí technologií v trutnovském závodě. Jak vypadá taková výroba v praxi?
Pokud je díl vyráběného produktu označen QR kódem, lze ho díky němu v jakékoliv části výrobního procesu jednoznačně strojově identifikovat. Kód je na jednotlivých pracovištích snímán a určuje, jaké úkony je třeba na daném pracovišti na výrobku provést. Současně je podle něj možné provádět kontrolu správnosti zpracování. Na serverové centrální uložiště se ke každému kódu průběžně ukládají procesní data. Celý výrobní proces je tak zdokumentován a detaily lze zpětně dohledat. Tím ovšem role QR kódu zdaleka nekončí. Pomocí aplikace pro chytrý telefon si může konečný zákazník z QR kódu finálního výrobku načíst podrobné informace o jeho parametrech. Tím se nejen snižuje možnost záměny, ale usnadňuje se tak i servis nebo proces generování zákaznické dokumentace.
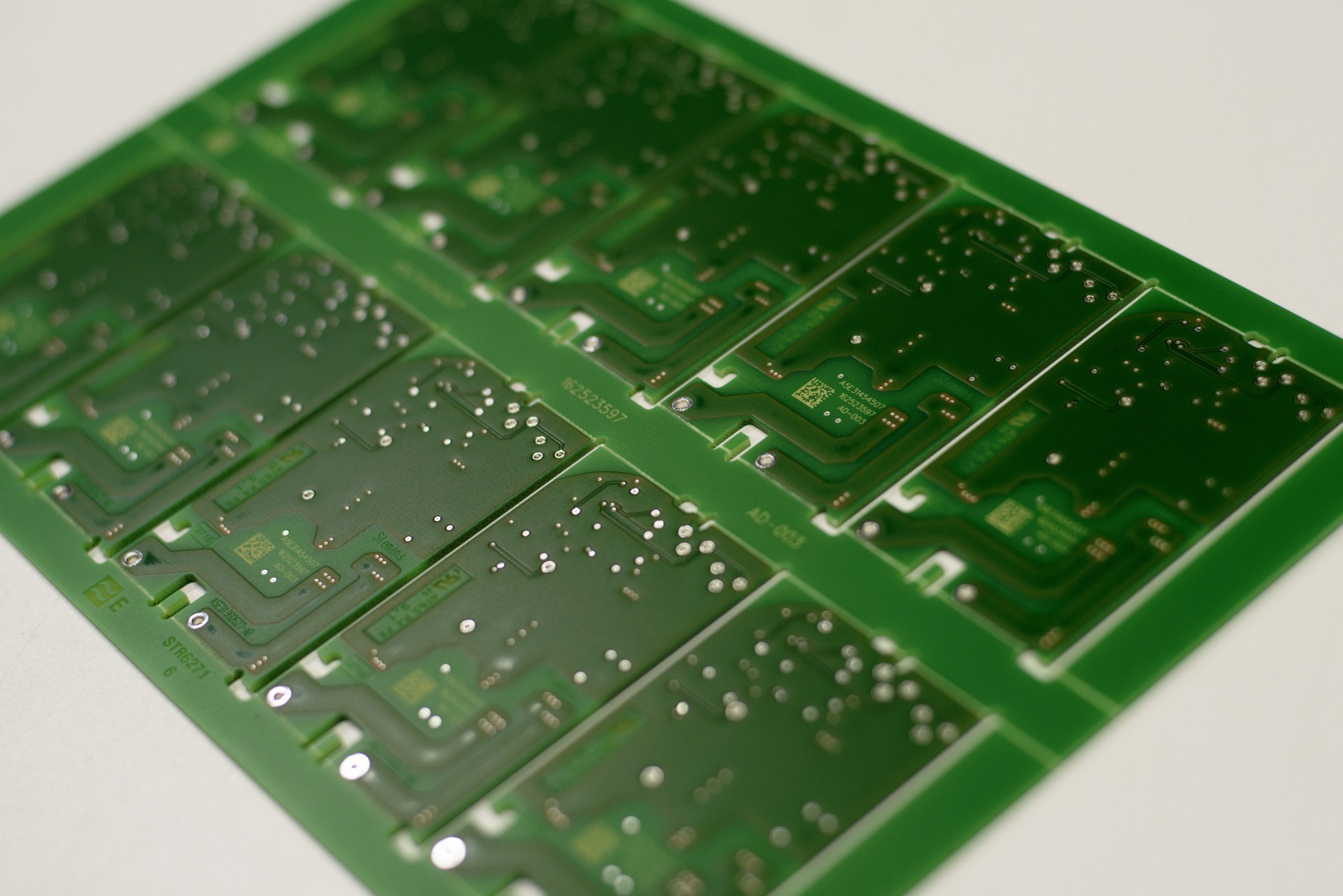
Aktuálně v Trutnově chystají zavedení nového výrobku, který bude vznikat na nové plně automatizované lince. Na ní budou jednotlivé kroky provázány a budou se navzájem kontrolovat. Jednotlivé moduly budou vyhodnocovat data z předchozí operace, a pokud všechny kontrolní znaky nebudou v pořádku, linka nedovolí zahájit činnost na dalším kroku.
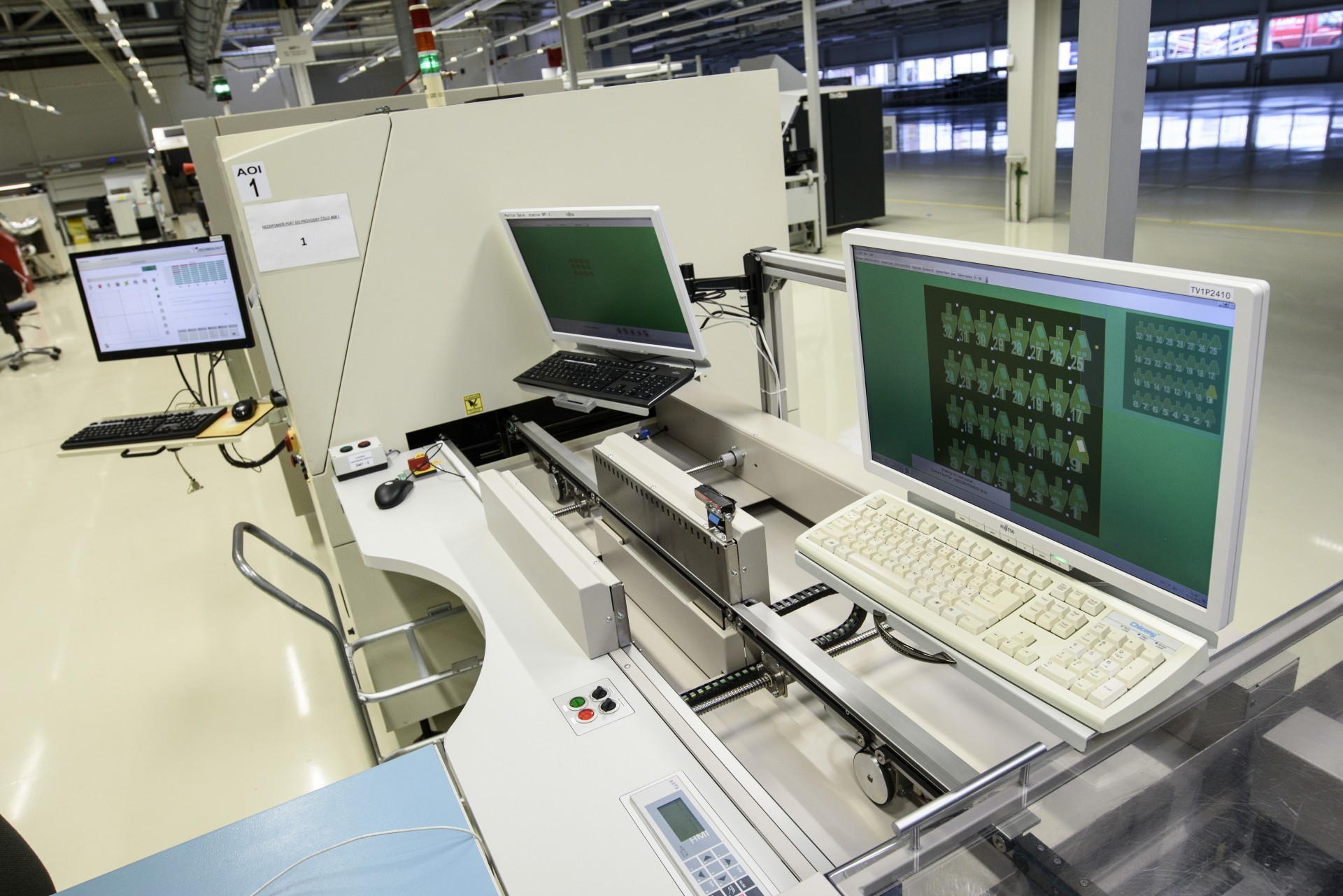
„Digitalizace se samozřejmě výrazně podepsala také na vývoji,“ upozorňuje František Mandát, vedoucí vývoje trutnovského závodu. „Díky ní může na novém produktu pracovat několik vývojových skupin současně, vedle České republiky třeba kolegové z Německa a Indie. To výrazně urychluje práci.“ Společným návrhovým systémem je zde NX od společnosti Siemens PLM Software a veškerá data – od jednotlivých dílů po charakteristiky finálních výrobků – jsou uchovávána v centrálním PDM systému (Product Data Management), takzvaném Teamcenter. Z dat, která vygeneruje vývojové oddělení při tvorbě plošného spoje, je vytvořen digitální 3D model. Na něm jsou přesně vidět součástky, čísla komponentů, i v jaké polaritě a na jakém místě mají být osazeny. Tato data se využívají pro přímou kontrolu ve výrobě. Obsluze je k dispozici aktivní digitální obrazovka, která zásadním způsobem usnadňuje práci. Dřívější papírové výkresy popisovaly osazení pro více variant výrobku, což bylo někdy obtížné pro orientaci. Nový 3D model zobrazí vždy jen tu správnou variantu. I díky tomu kvalita výroby celého řetězce překročila úctyhodných 96 %.
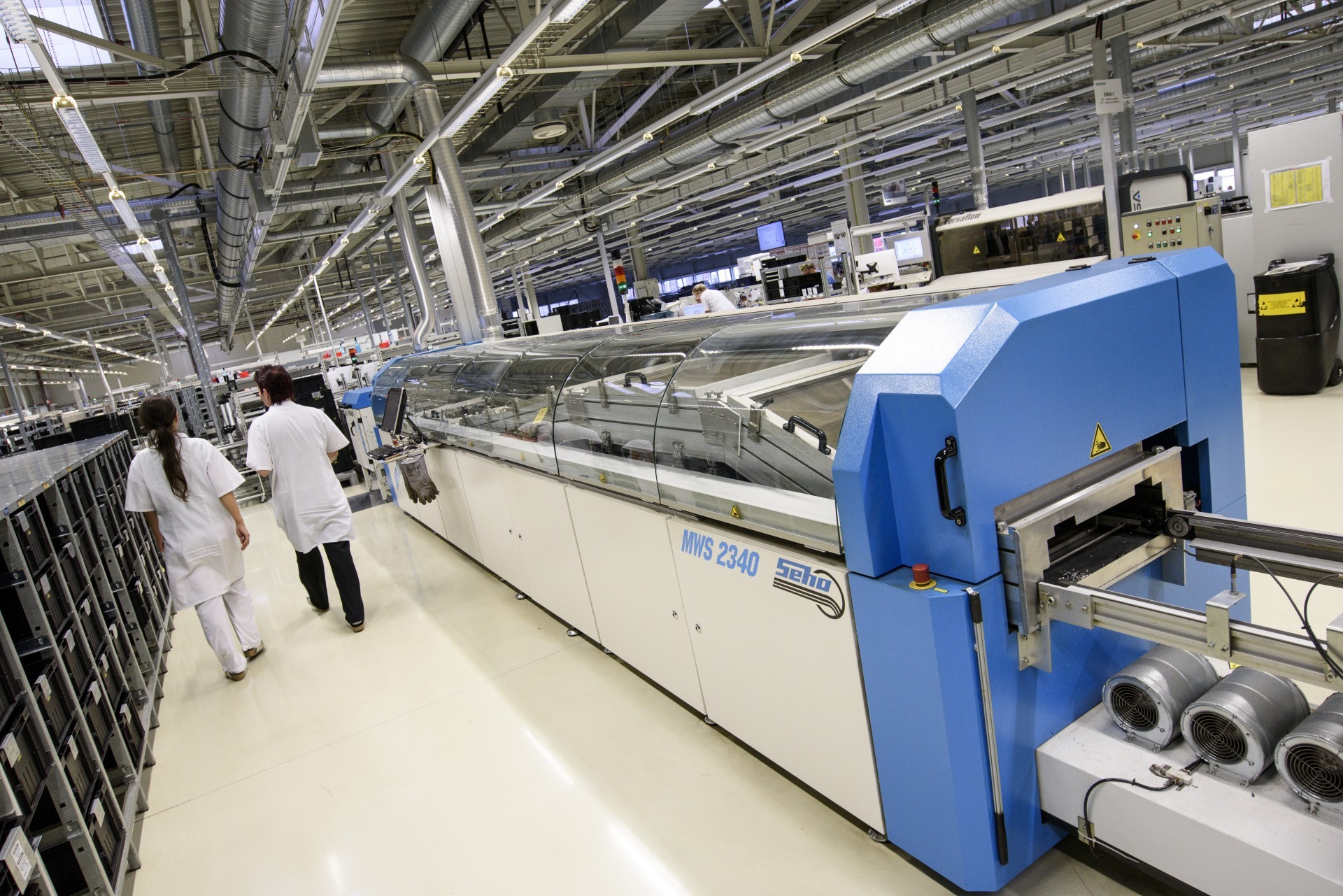
STAV VÝROBY V LETOHRADU HLÁSÍ OBRAZOVKY
V Letohradu pod Orlickými horami sídlí další součást koncernu Siemens společnosti OEZ. I zde jsou postupně zaváděny do praxe prvky Průmyslu 4.0. Podle Tomáše Jukla, vedoucího plánování technologie OEZ, jsou dobře patrny zejména ve výrobě vzduchových jističů nedávno převedené z Německa a na nové lince na výrobu kompaktních jističů. Již samotná koncepce řízení těchto výrob od počátku vycházela z principů Průmyslu 4.0.
Takřka každý výrobní úkon na nich řídí a kontroluje počítač. Princip je obdobný jako v Trutnově. Na každé významné podsestavě a na výrobku samotném je umístěn čárový kód, QR kód nebo RFID čip. Pracovní operace, ať již je prováděna na jednoduchém manuálním pracovišti, nebo na komplexní automatizované jednotce, začínají naskenováním kódu. Informace v něm uložená určuje, co bude s výrobkem provedeno. Systém vyhodnotí, jakou další operaci je třeba podstoupit a jaké dílce mají být použity. Ověří také kompletnost operací předchozích, zkontroluje jejich úspěšné dokončení a na závěr zaznamená důležitá procesní data do centrální databáze. Tam jsou uchována po celou dobu životnosti výrobku a jsou klíčovým zdrojem informací při řešení reklamací. Slouží také při analýze výrobních procesů a jejich efektivity. Tak přispívají k dalšímu zdokonalování výroby. Dalším přínosem digitalizace procesů je možnost neustálé kontroly a průběžného monitorování. Zvyšuje se tak využitelnost výrobních zařízení a při výpadku je možné rychleji reagovat. Na letohradských halách jsou dokonce rozmístěny obrazovky, které zaměstnance informují o aktuálním stavu výroby, plnění plánu a klíčových ukazatelích. Doplněno je i souhrnné zhodnocení ve formě semaforu. To má významný informační efekt a současně to motivuje tým. I Letohradští si pochvalují pozitivní přínosy myšlenek Průmyslu 4.0 při optimalizaci výroby, zlepšování kvality produkce a zvyšování komfortu a bezpečnosti práce. Při aplikaci v praxi vidí jako klíčovou hlavně spolupráci výroby, technologie a kvality. Pokud existuje shoda a vůle zde, technické řešení se dnes již určitě najde.
Zapojení dodavatelů i inteligentní roboty
Na závěr se vraťme ještě jednou do Mohelnice. Tentokráte do závodu Busbar Trunking Systems, kde se vyrábějí přípojnicové systémy pro moderní rozvody elektřiny. I zde se celým provozem prolínají prvky Průmyslu 4.0. Pilotní projekt bezpapírové výroby tu úspěšně zavedli již před třemi lety a současně jej rozšiřují o systém 3D modelů sloužících při výrobě trhem stále častěji žádaných individuálních řešení. Digitalizace, stejně jako v ostatních závodech, zásadně ovlivnila proces projektování výrobků. Zákaznické požadavky jsou dnes do výroby přenášeny s minimální potřebou lidského zásahu. Do budoucna se dokonce počítá s automatizací tohoto procesu až za hranice vlastní výroby. Individualizované požadavky potečou systémem bez lidského zásahu až k vybraným dodavatelům. Nová zařízení jsou pořizována s ohledem na jejich budoucí začlenění do konceptu automatizace. A jsou inteligentní... Umožňují například sledovat spotřebu a využití elektrické energie v jednotlivých úsecích výroby. A jsou inteligentní. Od léta zde funguje robotické balení palet a v únoru mají zprovoznit nový stroj na speciální ohyby. Ten na základě prvního kusu vyhodnotí vlastnosti materiálu a uzpůsobí tomu parametry ohybu u dalších kusů. Průběžně si přitom hlídá stálost vlastností materiálu a na změny reaguje.
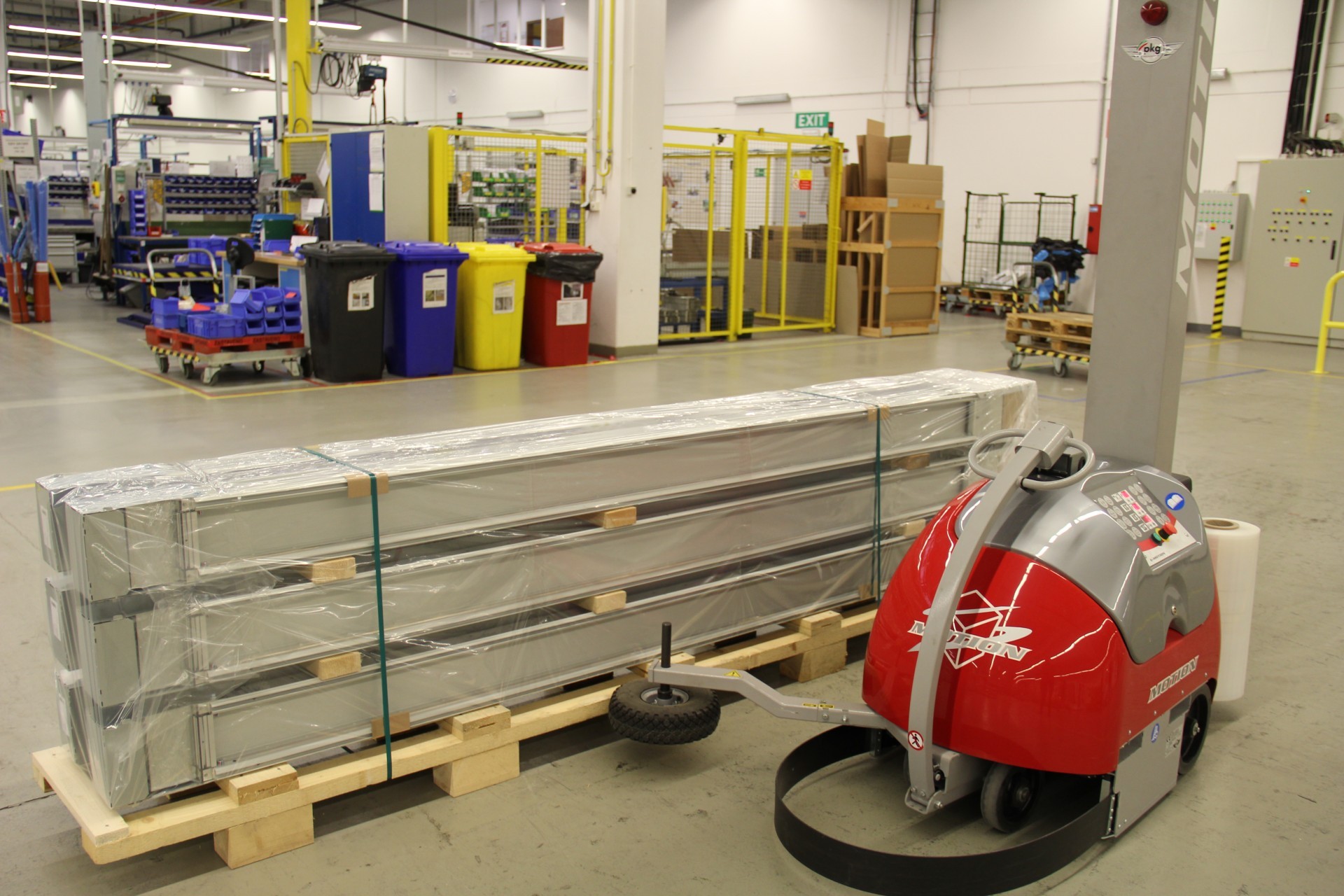