Jaké byly začátky projektu MindSphere v Mohelnici? Fungoval zde již před jeho spuštěním sběr dat?
Závod Siemens Elektromotory v Mohelnici je na velmi vysoké úrovni, takže sběr dat zde samozřejmě fungoval již před zavedením MindSphere a v tomto směru se neustále posouvají kupředu. Tyto informace ale pochopitelně nebyly dostatečně detailní; jednalo se hlavně o sledování dostupnosti strojů, tedy o spojování konkrétní zakázky s daty ze stroje. Implementace MindSphere pak přidala kompletní přehled o výrobě i o jednotlivých strojích. Tento projekt běží v Mohelnici již od konce roku 2018, kdy se tento závod připojil do testovacího oddělení Cloud Customer Support.
Které pracoviště bylo zapojeno do systému MindSphere jako první a jaký je stav k dnešnímu dni?
Prvním pracovištěm, které bylo připojeno již koncem roku 2018, bylo pracoviště odlévání rotorů. Díky této aktivitě si v Mohelnici mohli vyzkoušet způsob sběru dat do cloudu a možnosti této Siemens platformy. Jelikož se toto řešení osvědčilo a v Mohelnici pochopili, jak velkou perspektivu má, rozhodli se pro zavedení velkého balíčku Connect & Monitor, s jehož implementací se začalo v létě 2019. Jednalo se o projekt, který se realizoval ve spolupráci s MindTeam v Německu, nicméně fyzické připojování zajišťovalo oddělení Siemens Customer Services. Do konce roku 2019 se podařilo připojit všech 36 obráběcích strojů z obrobny a nyní se pracuje na připojení dalších dvanácti důležitých automatických navíjecích pracovišť. Všechno tyto stroje mají v rámci jednotlivých technologií pro Mohelnici klíčový význam a velký vliv na hlavní KPI ukazatele indikující schopnost plnit požadavky zákazníků.
Máte již k dispozici první výsledky, které by ukazovaly přínos nasazení tohoto systému? Můžete uvést konkrétní příklady?
Díky tomuto velkému projektu se již v Mohelnici podařilo realizovat hotové vizualizace pro sledování výroby. Tyto dashboardy se již začínají pilotně používat v oddělení Business Excellence. Velkou výhodou je, že nyní mají mnohem víc informací, než tomu bylo doposud s lokálním systémem. Podle slov projektového specialisty ze závodu Elektromotory Mohelnice Valentina Kósy „vizualizace v Mohelnici umožňují přímo sledovat klíčové informace o stavu stroje a délce trvání daného stavu, je možné si zobrazit vývoj produktivity – počty vyrobených produktů, a to podle časového rozdělení anebo podle konkrétního výrobku. Dále pak lze sledovat dostupnost stroje během zvoleného dne, kde můžeme mít vše rozděleno na směny. Je to kompletně vytvořeno závodu na míru, přesně podle požadavků pracovníků z výroby. Nejedná se tedy o žádné obecné řešení – sám uživatel si vybírá, jaká vizualizace ho v daném okamžiku zajímá“.
Na začátku projektu jsme také zorganizovali Ideation Workshop, na který dorazili odborníci z Německa. Ti prošli s pracovníky závodu v Mohelnici veškeré procesy a vytyčili cíle balíčku Connect & Monitor přesně Mohelnici na míru. V rámci toho byla také identifikována oblast prediktivní údržby, která zatím využívá sledování stavů klíčových uzlů zařízení, například vibrace oběžných kol ventilace u lakovacích linek.
Jaké máte v rámci tohoto projektu další plány do budoucna?
Aktuálně pracujeme na připojení zbylých strojů z navijárny, které by mělo být dovršeno do konce léta 2020. Dále se pak v Mohelnici interně vytváří vizualizace pro oddělení podpory výroby a údržby. Samozřejmě ale pracujeme především na dalším rozvoji, který představuje následný krok v rámci digitální transformace továrny – intenzivně jednáme o balíčku Analyze & Predict, který obsahuje možnost vytvoření algoritmu na míru, který by využíval strojové učení, principy neuronové sítě a další prvky umělé inteligence. V oblasti digitalizace chce být mohelnický závod, stejně jako další závody Siemens, na špici.
Co by implementace tohoto balíčku konkrétně znamenala?
Ve spolupráci s odborníky z MindSphere Team najít konkrétní řešení prediktivní údržby na základě historických dat a posunout procesy údržby z operativního systému do prediktivního s plánovanou časovou i kapacitní odstávkou strojů pro potřebné opravy, a to na základě vizualizovaných dat z celého stroje.
Bude uživatelské rozhraní vyvinuté pro mohelnický závod využitelné i v jiných závodech, nebo se jedná o unikátní řešení na míru?
Uživatelské rozhraní je vždy vytvářeno přesně podle požadavků budoucích uživatelů (např. oddělení výroby a údržby) a na základě možností dat, která se sbírají ze strojů. V mohelnickém závodě pracují stroje různých typů, proto se sběr dat i jejich analýza a následné zpracování v cloudu musí řešit individuálně. Tato data pak umožňují vytvářet vizualizace na míru přesně podle požadavků konkrétních lidí ve výrobě. Vizuální stránku, tedy vzhled a zobrazovací prvky, ale pochopitelně lze využít a rozšířit i v jiných závodech. Ovšem logika zpracování dat by se musela naprogramovat jinak (na míru podle vybraných strojů). Je ale pravda, že Mohelnice plánuje využívat pro analytiku a práci s daty v cloudu budované kapacity Siemens HUB Ostrava a připravené řešení co nejvíce využívat i v ostatních lokacích s minimální customizací.
Přepokládám, že nasazení MindSphere v Mohelnici úzce souvisí s vývojem digitálního dvojčete elektromotoru. Jaký je aktuální stav tohoto projektu?
Ne zcela; plné digitální dvojče motoru, na kterém pracuje konstrukční část Siemens HUB Ostrava a R&D v Mohelnici, bude sloužit ke zkrácení vývoje nebo řešení a k ověření zákaznických požadavků na stávajícím produktu. Propojení do cloudu MindSphere se tak automaticky nabízí jako řešení procesu sběru a vizualizace dat. V budoucnu pak bude možné sledovat parametry motorů přes vzdálený přístup přímo u zákazníka – od monitorování nákladů až po plánování servisu. Nasazení MindSphere v Mohelnici má dva hlavní cíle: digitalizaci procesů dvou identifikovaných oblastí – dostupnosti strojů a prediktivní údržby.
Je v plánu a lze reálně uskutečnit kompletní napojení mohelnického závodu na MindSphere, čímž by se stal výrobním závodem podobným závodu Siemens v Amberku?
Myslím, že Amberk je pro mohelnický závod velkým vzorem a začíná se mu postupně přibližovat, což mě velmi těší. V plánu je samozřejmě systém postupně rozšířit na další pracoviště. Tradiční mohelnický závod ale samozřejmě má i pracoviště, která nedisponují odpovídajícími technologiemi. Zde připojení nejspíše nebudou zvažovat. Naopak, nově pořízené technologie se budou připojovat do cloudu MindSphere automaticky. V Amberku čerpá Mohelnice i zkušenosti týkající se rozšiřování personálních kapacit pro rozvoj digitalizace a krok za krokem buduje vedle klasické technologie také oddělení vývojové technologie, jehož součástí jsou i experti na cloud a vizualizaci dat pro potřeby jednotlivých útvarů přímé výroby a servisu.
Je těžké modernizovat takto starý závod s dlouhou tradicí? Je to překážka?
Mohelnice je závod s dlouho historií, na kterou jsou místní velice hrdí, ale dnes nemůžeme mluvit o stáří, protože Siemens do Mohelnice v minulých letech intenzivně investoval, jak do infrastruktury hal, tak do technologií, a nyní se aktivita upírá právě do oblasti digitalizace a automatizace. Obecně bych řekla, že závody Siemens jsou na tom v porovnání s ostatními továrnami v České republice vcelku dobře. Pravda je, že jsme u strojů v závodě často bojovali s vybavením a možnostmi aktuálních technologií. V některých případech je potřeba dovybavit pracoviště buď novou senzorikou pro potřebné veličiny, nebo komunikačními prvky pro možnost připojení a sledování.
Jak řešíte nové nároky na kvalifikaci nejen obsluhy strojů, ale také na nové pozice, které s sebou digitalizace přináší?
Velice dobrá otázka! V Mohelnici probíhá současně s procesy digitalizace a automatizace proces zaškolení současných pracovníků na nové systémy nebo technologie. Každý digitalizační nebo automatizační projekt obsahuje manuály pro danou oblast obsluhy strojů, podle kterých se učí nejen pracovníci odborných a servisních útvarů, ale hlavně pracovníci ve výrobě, jak s novým řešením pracovat. Zavádějí se i podpůrné procesy, jako například nový mzdový motivační systém, v rámci, kterého každá změna pracoviště prochází analytickým hodnocením za účasti zástupců odborové organizace. Výsledky tohoto hodnocení mohou přinést i nárůst příjmů z důvodu nutnosti vyšší odbornosti. Pracovník se pak může pohybovat v rámci jedné třídy od úrovně začátečník až po úroveň expert. Poslední částí je pak příprava interního školicího systému pracovníků výroby, který jim má pomoci, aby zvládli přechod na nové technologie.
Současná koronavirová pandemie, kromě jiného, významně ovlivnila digitalizaci napříč všemi lidskými činnostmi. Vidíte v digitalizaci mohelnického závodu další konkurenční výhodu z hlediska možnosti vzdálené diagnostiky a řízení apod.?
Určitě, myslím, že tato nová situace ohledně onemocnění covid-19 mnoha výrobním závodům a firmám otevře oči. Pochopí, že digitalizace je opravdu potřeba a že je nutné automatizovat výrobu a ukládat data do cloudu, protože jen tak pak lze vše sledovat třeba z pohodlí domova. V těchto dnech, kdy je velké množství pracovníků na home office, je velmi výhodné mít možnost připojit se do cloudového operačního systému z domu a podívat se na aktuální nebo na včerejší chod výroby na připojených pracovištích. Mohelnice digitalizovala 100 % všech pravidelných jednání, elektronicky řeší pravidelný GEMBA meeting a možnosti digitálních řešení využívá opravdu naplno. Budoucnost je v několikaúrovňovém výrobním, technologickém a logistickém informačním systému, kde se zobrazují data v detailech pro danou úroveň řízení a kde je od nejnižší úrovně stroje management upozorňován na výpadky ve výrobě, kde si lze přes digitální systém přivolat servis, ověřit dostupnost ND ve skladu, případně vystavit automatickou objednávku a dle termínu dodání naplánovat odstávku stroje pro servisní zásah.
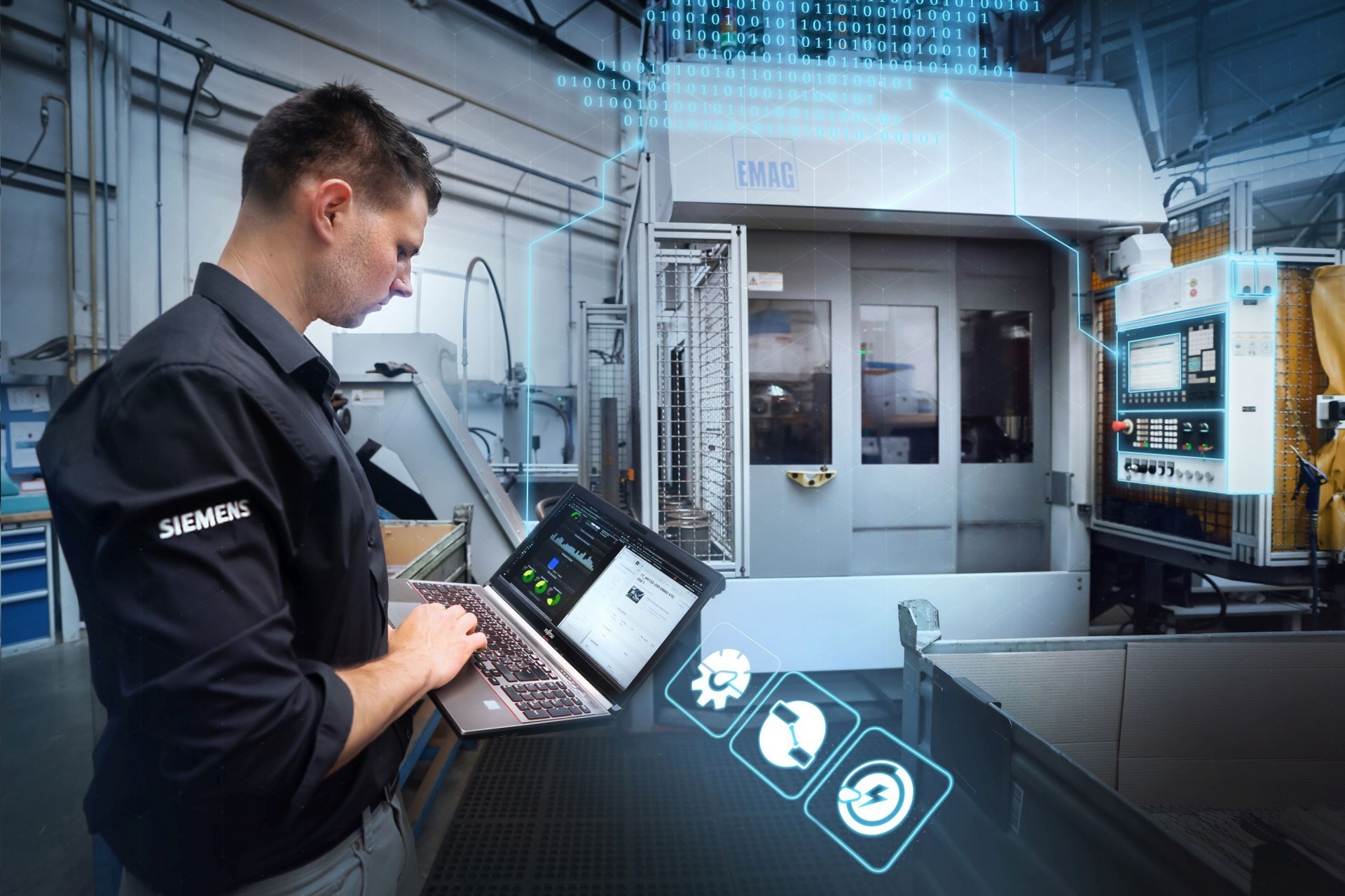
Princip zapojení a sběru dat Mindsphere
Systém MindSphere byl v Mohelnici pilotně nasazen na pracovišti odlévání rotorů velkých osových výšek, a protože se osvědčil, na podzim roku 2019 bylo zapojeno dalších 36 klíčových strojů. Fyzické připojení výrobních strojů a následný sběr dat do cloudového prostředí realizuje oddělení Siemens Customer Service. Skupiny strojů jsou rozděleny podle výrobních hal a data se z nich sbírají do tzv. Master PLC, kde se předzpracovávají a následně se posílají pomocí hardwarového komponentu MindConnect Nanobox do MindSphere. Již dnes sběr dat a jejich vizualizace v mohelnickém závodě přispívají velkou měrou k optimalizaci procesů. Jde například o vyhodnocování různých nestandardních stavů, jako jsou vibrace či teplota, které pomáhají i při plánování údržby. Výsledkem je tedy minimum havarijních stavů strojů s dlouhým termínem opravy. Takové závady jdou mnohdy do milionů korun a vedou ke zpoždění dodávek či dokonce ke ztrátě zákazníků. Další důležitou datovou základnou jsou informace o parametrech stroje, jako je navolení programu obsluhou, spuštění cyklu, taktu stroje, otáček vřetena apod. To všechno jsou data, která slouží k další optimalizaci například ztrátových časů při výrobě, navyšování kapacity a efektivity či standardizaci výroby. Pomocí těchto nástrojů lze také postupně zkracovat průběžnou dobu výroby, což je v dnešní době jeden z klíčových parametrů štíhlé výroby a nezbytný požadavek trhu na rychlé dodání a flexibilní reakci v oblasti výroby. Pomocí digitální vizualizace na míru se v Mohelnici daří na tyto stavy a trendy trhu reagovat patřičně rychle a efektivně.
Uživatelská vizualizace a monitorování dat u obráběcího stroje na pracovišti předmontáže
„Na obráběcím stroji na pracovišti předmontáže se monitorují základní informace o stroji během výroby. Na uvedených příkladech lze vidět shrnutý přehled stavů zařízení pro rychlou informaci pro kolegy z výroby. Následně je možné detailněji analyzovat stav zvoleného zařízení. Vizualizace vytvořená pro kolegy z výroby zobrazuje podrobnější informace ohledně dostupnosti a produktivity na zvoleném pracovišti, rozdělené dle směn. Druhá vizualizace slouží pro kolegy z oddělení údržby, kde mohou kontrolovat průběh sledovaných veličin ze stroje (proudové zatížení, teplota, rychlost pohybu os) za zvolený časový interval. Vizualizace jim rovnou vyhlásí, kdy a kolikrát daná veličina překročila předem definovaný limit. Aktuálně se v rámci DT – vývojové technologie – pracuje na detailnějších vizualizacích a dalších funkcionalitách systému. Cílem je vytvořit digitální profil stroje, který umožní vytvořit systém hlášení predikovaných poruch a bude poskytovat výstupní informace potřebné pro výpočet OEE a další nezbytné analýzy, které budou při své práci používat hlavně oddělení přípravy výroby, údržby a výroby,“ popisuje Valentin Kósa.